Direct Air Capture
Carbon Dioxide Removal (CDR) technologies can assist in decarbonising hard-to-abate sectors and addressing historical emissions to enable industries to get to the net zero emissions goals. These technologies enables carbon removal from the atmosphere and while they are one of the hottest areas of climate research but they are also the most controversial ones.
The CDR technologies include:
-
Direct air capture (DAC)
-
Enhanced mineralization
-
Afforestation and reforestation
-
Bioenergy
-
Agricultural soil carbon sequestration​
Climate Cure is focusing on developing a practical and cost effective Direct air capture technology. The commercialization of CO2 capture from ambient air began in the 1950s for pre treatment of air for cryogenic air separation. In the 1960s, it was thought that CO2 might be captured from the air and used as a feedstock for mobile nuclear power for production of hydrocarbon fuels at remote military bases. In the 1990s, Klaus Lackner suggested the utilization of large-scale capture of CO2 from air as a climate change mitigation toll.
The biggest challenge of the direct air capture is low CO2 concentration in the air which will require higher energy demand compare to other available point source technologies as seen in the image below. The challenge raises opportunity for new and advanced concepts to reduce the energy demand and cost of the process.
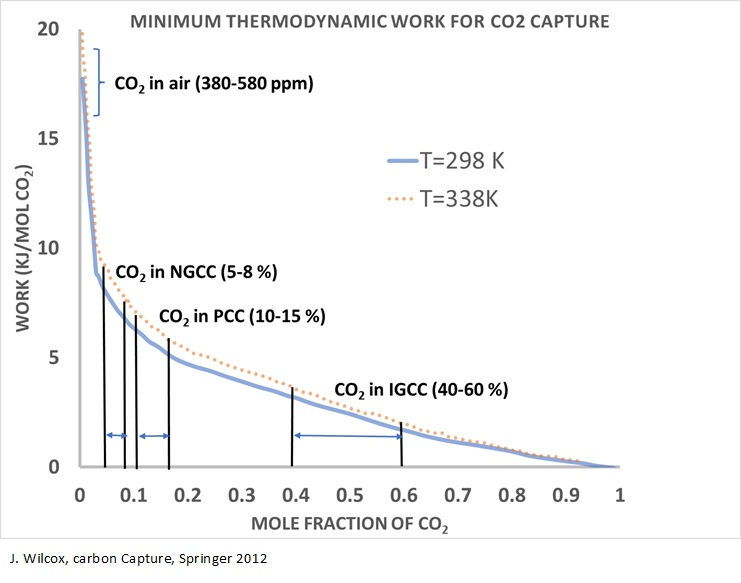
Climate Cure is taking on this challenge and in collaboration with University of Calgary and licensing their advanced solid adsorbent for direct air capture process. Climate Cure is taking a traditional process engineering practices by integrating DAC with CO2 conversion to gasoline process for minimizing energy dependency and reducing energy intensity of DAC process.

The integrated process will enable corporates to capture the CO2 from atmosphere and convert it to e-fuel and replace the fossil fuels using a cost effective and practical processes. This concept not only will avoid CO2 generation by replacing fossil fuel, it will create opportunity for energy independency for countries which have been dependent in fossil fuel import for a century while creating jobs and activities in micro economic scale.
Bio gas, Landfill Gas Processing and CO2 Utilization:
Climate Cure's approach is to establish a flexible business model to ensure the ability to respond to fast-changing market dynamics. Climate Cure will utilize a platform technology to produce a product that can be used as a building block for many other industries. This would provide an opportunity to produce various end products depending on the market needs using the same platform technology and infrastructures.
The platform technology adopted is reforming bio gas, or landfill gas or carbon dioxide and methane to produce syngas that can be used for production of sustainable aviation fuel, e-fuel or methanol.
Sustainable Aviation Fuel
Aviation transportation is one of the sectors that are hard to abate for decarbonization. The proposed solutions for decarbonization can take a long time till they become competitive and practical, solutions such as electric airplanes or hydrogen-based airplanes. An interim and fast solution for the decarbonization of aviation transport without waiting for the development of alternative technology is the use of sustainable aviation fuel (SAF).
SAF is a type of jet fuel that is made from renewable sources; in our case, it will be produced from biogas or landfill gas or captured CO2 from processes such as direct air capture or point source using our Tri-Reforming process for conversion to Syngas and in combination with traditional Fisher Tropsch to SAF. It can be blended with conventional jet fuel and used in existing airplanes without any modifications to the engine.
Here are some of the benefits of using SAF:
-
Reduces greenhouse gas emissions: SAF can reduce lifecycle greenhouse gas emissions by up to 80% compared to conventional jet fuel. This is because the feedstocks used to produce SAF absorb carbon dioxide from the atmosphere as they grow.
-
Reduces dependence on fossil fuels: SAF can help to reduce the aviation industry's reliance on fossil fuels, which are a finite resource.
-
Air quality improvements: SAF can also help to improve air quality by reducing emissions of pollutants such as particulate matter and nitrogen oxides.
There are still some challenges associated with SAF, such as the fact that it is currently more expensive to produce than conventional jet fuel. However, we expect our novel Tr-Reforming process to produce cost-effective SAF products.
E-Fuel Production
Nations at COP28 in Dubai approved a roadmap for transitioning away from fossil fuels, this can be a tectonic move in energy market, which can affect investments, developments and future of the energy sector. Lack of alternative global scale clean fuel options divided the nations on the language used on the agreement.
The energy transition to alternative energy sources are in a global scale and requires a global solutions. Renewable energies are suffering from limitations imposed by availability of natural resources and form of the energy produced as electricity. Delivery of electricity to the users requires infrastructure and its use for mobility, will be limited to availability of resources to produce batteries. This raises a big risk for energy transition.
One of the options for a smooth transitioning from fossil fuel is to replace them with E-Fuels. E-fuels, like e-methane, e-kerosene and e-methanol, are all fuels in gas or liquid form that are produced from renewable (solar or wind power, for example) or decarbonized electricity and CO2. E-Fuels have capability to drastically reduce the harmful emissions associated with combustion engines. E-fuels will play a key role in energy transition strategies. Taking their whole production cycle into account, their carbon footprint is a lot lower than oil-based fuels. Even after EU officially banned the sale of new passenger cars and vans using internal combustion engines (ICE) from 2925, Germany and Italy supported the sale of ICE vehicles which run on e-fuel or CO2 neutral fuels after
How are they produced? Liquid e-fuels: like e-methanol and e-crude, also known as synthetic crude oil, are made from capture CO2 and renewable electricity. E-fuels are form of synthetic hydrocarbon which are mixture of hydrogen and carbon. The source of carbon for this process are from captured CO2 from air or from point sources and typically the hydrogen comes from electrolysis of water from renewable electricity. The mixture of CO2 and H2 goes through few steps of high temperature processing steps to produce an e-fuel. At some cases the carbon in e-fuel is replaced with Nitrogen to produce synthetic ammonia (NH3) as e-fuel.
Heavy mobility accounts for about a quarter of global CO2 emissions. With this in mind, and at a time when electricity would appear to be the future of road transport, e-fuels have a key role to play, particularly in the maritime and air transport sectors for which decarbonisation cannot be achieved solely through electrification.
E-fuels have the advantage of using the same infrastructure as their fossil equivalents (petrol, diesel, kerosene, methanol or natural gas).
Advantage of our Re-Fuel TM compare to e-fuel:
For our Re-Fuel TM production we are using a process called Dry Methane reforming to use natural gas as a source of hydrogen. In this process there is no requirement for electrolysis process for hydrogen production. This reduced the dependency to another sacred resources which is clean water and reduce the production cost.
Our Re-Fuel TM production can be integrated into solar, wind or geothermal operation for its own energy requirements.

Propene (Propylene):
Propene (often known as propylene) is a very important building block for a large number of chemicals, including the addition polymer, poly(propene). Propene is primarily used as a monomer in plastic production. It is also used to prepare other chemicals, as a fuel additive, a fragrance, or a perfume ingredient. Below are statistics of global use of propene:


Production of propene:
Traditionally propene was produced utilizing two processes:
-
Steam cracking of naphtha
-
Catalytic cracking of gas oil
These two traditional processes produce ethene together with propene. This created a need for more advanced processes for higher selectivity for propene production.
-
Catalytic cracking of propane: Increasingly, propane is being catalytically cracked to form propene,
-
The MTO (Methanol to Olefins) process: Another process that has been developed is via methanol (produced from biomass via synthesis gas), the MTP (Methanol To Propene) process which is an example of the MTO (Methanol To Olefins) process.
The MTP will be the selected technological pathway for climate cure for producing propene from methanol.
Methanol:
Methanol is produced from synthesis gas (carbon monoxide and hydrogen), traditionally derived from oil, coal, or biomass.


The largest use for methanol is as a feedstock for the plastics industry. Another major use of methanol is producing plastics derived from methanal. Methanol is the feedstock for producing methanal and a variety of plastics, based on reactions with phenol, carbamide (urea) and melamine. The production of polymers such as the polyester Terylene uses methanol as the original feedstock.
A most remarkable increase is in the use of methanol to produce alkenes by the MTO and MTP processes. This will pave the road for a large proportion of plastics such as poly(ethene) and poly(propene) will, in the near future, be derived from synthesis gas.
Methanol is destined to be a major fuel for cars, either as a liquid fuel, mixed with petrol, or in fuel cells where it has been used to prepare, in situ in the car, hydrogen for the fuel cell.
The methanol can be converted to other fuels such as gasoline using the MTG (methanol to gasoline) process. Methanol is converted into alkanes and aromatic hydrocarbons suitable for petrol (hydrocarbons with 5 to 8 carbon atoms), by using thermos catalytic reactions. If CO2 is the feedstock for syngas production and renewable energy is used for the process the product will be e-methanol and the final product will be e-fuel.